Наша головна мета – повне задоволення потреб споживачів. Продукція Марилівського МПД повністю відповідає державним стандартам і вимогам наших партнерів. Ми гарантуємо високу якість не лише продукції, але й усіх послуг, що надаються замовникам: консультації щодо купівлі, організація доставки та інші супутні послуги.
Досягнення високої якості нашої продукції забезпечується за рахунок:
- впровадження новітніх технологій;
- підбору висококваліфікованого персоналу;
- автоматизації виробничих процесів;
- використання найсучаснішого обладнання.
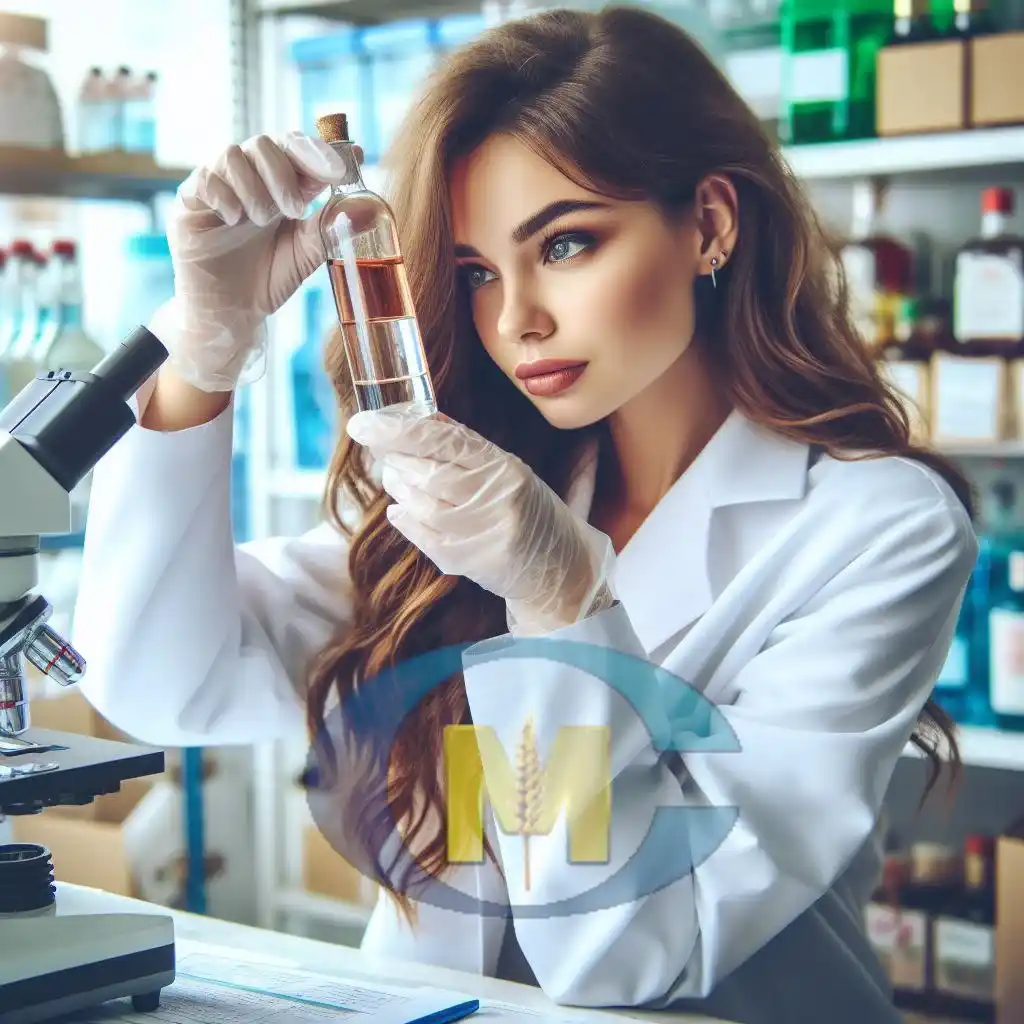